Turning fallen leaves into paper — what may sound like a wild idea at first has evolved into an award-winning business model with huge potential for the circular economy. In the following interview, the team at Releaf Paper shares how a student science project grew into a sustainable alternative to traditional papermaking — and where their journey is headed next.
Let’s start with the basics — what exactly is Releaf Paper, and how did the idea of making paper from leaves even come about?
Story of Releaf Paper begins in 2017, when 16-year-old Ukrainian biotechnologist Valentyn Frechka created the first hand-made paper castings using fallen leaf fibers in his home laboratory. This success served as the basis for further research into the use of leaves. In 2021, Releaf Paper was founded, where Valentyn became one of the founders and head of technology. The France-based company continued R&D of leaves as a material, while working to bring its products to market. Fundamental research in the laboratory of Grenoble (France) completed the result of 6 years of work — Releaf Paper has created a scientifically proven technology for isolating fallen leaf fibers for use in paper production. The first products of the company, which is managed by one of the founders and CEO Alexander Sobolenko, have been successfully tested in a number of EU countries, and in 2024, the company opened its first industrial leaf processing pilot production near Paris.
We’re used to thinking of paper as coming from trees — when did you realise leaves could be a game-changer in the recycling world?
Valentyn Frechka, born in Ukraine’s Zakarpattia region, came up with the idea during his time as a student at the Junior Academy of Sciences. While working on a research project, he set out to find alternative sources of cellulose. He initially explored agricultural waste like flax and straw but eventually turned his attention to other types of plant waste. Being someone who often spent time in the forest, he started considering fallen leaves. The idea didn’t come from a park stroll — it developed through structured research, but it was inspired by his close contact with nature. After months of lab work, he confirmed that leaf fiber had the right qualities for papermaking, and that’s where the Releaf Paper concept began.
What kind of leaves are we talking about here — and how do you actually turn urban leaf waste into high-quality paper?
We actually use almost all urban leaves in Europe and had a lot of tests with different kinds of green waste, for example pineapple leaves, and it works. The patented technology created by Releaf Paper allows the use of various methods of processing green biomass — from mechanical to thermo-chemical. The combination of different techniques makes it possible to obtain various products, from filler to full fiber with paper-making properties. This makes it possible to use these materials for a variety of applications: paperboards and containerboards, injection-molded containers, hygienic paper, bioplastics, etc. Both as the main raw material in its own right and as an additional component in combination with other types of fibers — recycled fibers or virgin wood.
In addition, the technology is flexible to different types of raw materials, allowing us to process stems of agricultural waste, grapes, and flowers in addition to leaves. Besides, the Releaf technology has been successfully used to valorize pineapple and palm frond waste.
Fillers created by mechanical processing are already produced by Releaf Paper in industrial volumes, while thermo-chemical fibers are undergoing the last stages of validation before mass production.
How does Releaf Paper compare to traditional paper when it comes to environmental impact, carbon footprint and resource use?
The company’s core product is Releaf Filler, a filler made from fallen leaves that is used to produce certain paper models by blending them with recycled fibers. The main consumers of the product are paper mills.
For manufacturers of paper packaging, the company offers several models of its own Releaf Paper brand of craft paper, from 80 to 170 g/m², which they use to produce bags, corrugated products, envelopes, and wrappers.
The company offers brand owners and retailers ready-made packaging solutions — from craft bags to boxes, and customization is available for larger volumes.
All Releaf Paper products are, of course, made using fallen leaves as the main ingredient, and without harming the environment.
Impact
– Only 0.066 kg CO₂ per kg during production (up to 70% lower compared to average* — global markets, open data)
– Only 0.002 l of water per kg during production
– <20 km logistics of raw materials
– 1 year time of restoration
– 55 days time of biodegradation
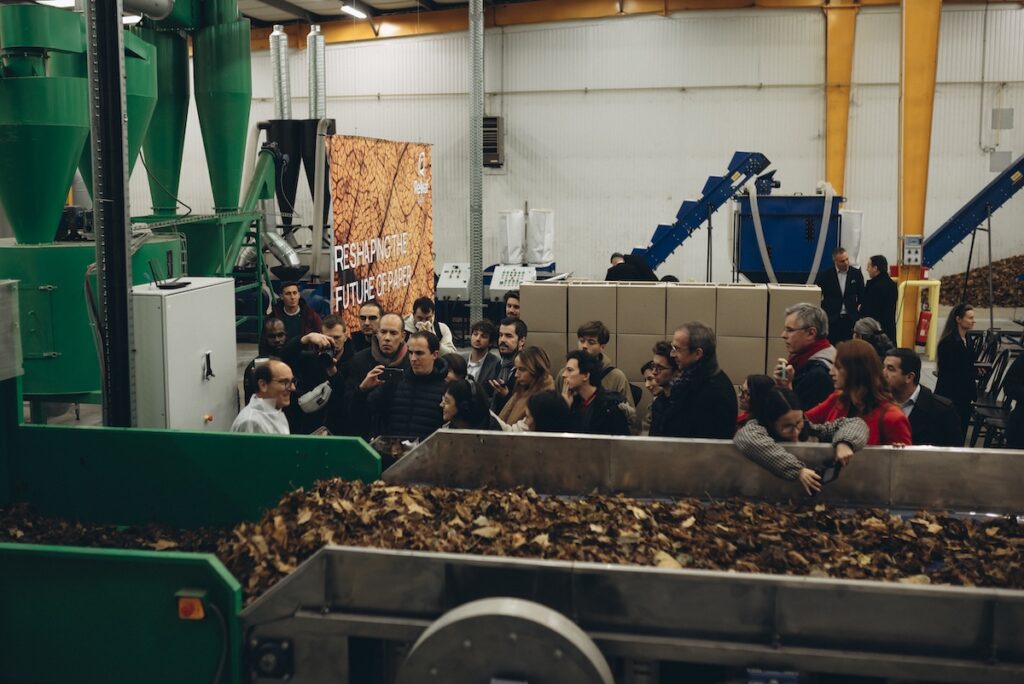
What were the biggest technical or logistical hurdles in creating a scalable leaf-based recycling process?
We have to make agreements with a variety of different partner cities in different countries to secure raw material availability.
Let’s talk scalability — how big could Releaf Paper realistically get, and what’s your vision for the next few years?
The company’s further development is to expand its local green waste recycling activities in other countries. To this end, Releaf Paper plans to set up at least 5 recycling facilities in Europe over the next 5 years. After that, the company plans to enter the US, Canada and Japan. In addition to green waste, Releaf Paper also plans to use agricultural waste, such as vegetable stalks, vineyard stalks, flowers, tropical fruits, and palm leaves.
Future business areas that Releaf has begun to explore based on its extensive knowledge of green waste include hygiene products, energy, and bioplastics.
In 2025, the company plans to raise at least €8 million in a Series A round.
A lot of startups aim to disrupt — do you see Releaf Paper more as a disruptor, or as a complement to the existing paper industry?
Yes, we really started as disruptors because we were full of enthusiasm and energy. Now we are more reality-based, because it is difficult to disrupt something that has been working for hundreds of years and is worth 350 billion dollars a year. That’s why we are more of those who do not let the paper industry rest in peace.
How do you source the leaf waste — do you partner with municipalities, or is it more of a decentralized model?
We use all opportunities. Because even in France every municipality has its own process of utilization of green waste. So, yes, basically we start with negotiations with municipalities and then try all other options including private subcontractors.
Can you share any stories from early adopters or brands using Releaf Paper that really surprised or inspired you?
As soon as we announced that we had started producing paper from leaves, we were approached by L’Oréal, Weleda, Samsung, and Ariston within a few weeks. It was extremely pleasant, especially in the case of L’Oréal, because their COO had been trying to contact us for more than a month, and he finally succeeded. In 2 months, we fulfilled the first orders for all of the above brands.
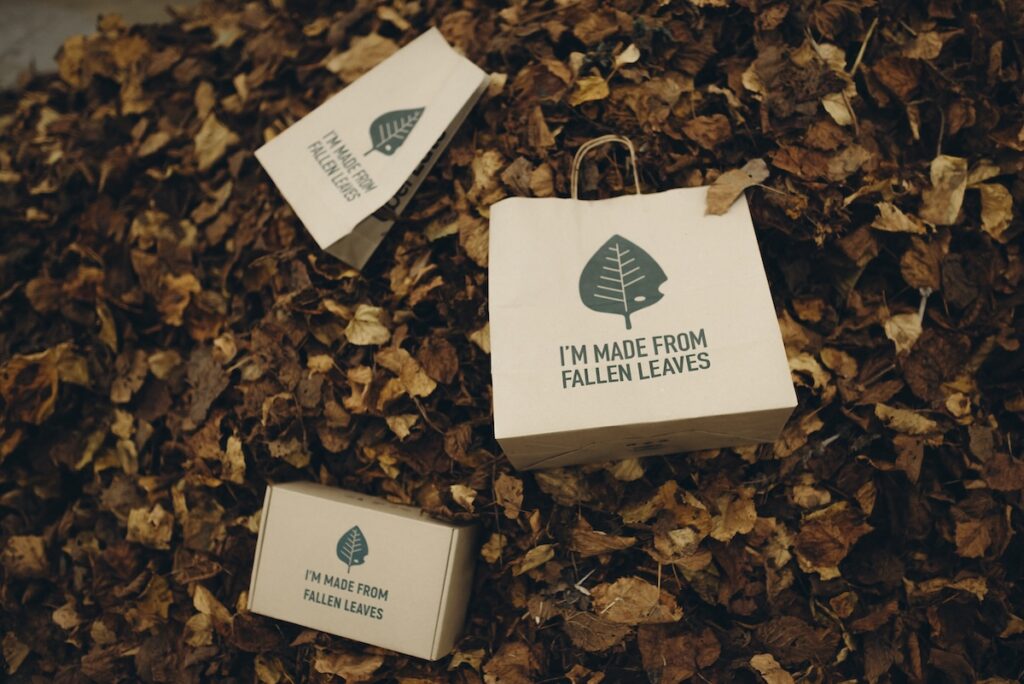
You’ve won awards and attracted media attention — how do you stay grounded while building something with such massive potential?
Releaf’s commitment to the circular economy was recognized and awarded by WWF, Canopy Planet, Google for Startups, EBRD, LVMH Innovative Award, and a series of Sustainability Awards. In 2024, Releaf’s technology became the 2nd best invention by the European Patent Office. In 2025, Releaf Paper was selected as a finalist in the Cellulose Fibre Innovation of the Year Award by nova-Institute, recognizing our breakthrough in turning fallen leaves into high-performance packaging. Additionally, we were honored with the ALL4PACK Innovation Award 2024 in the Innovative Materials category, highlighting our commitment to eco-friendly packaging.
While these accolades are gratifying, they serve as milestones rather than endpoints. Our focus remains on the continuous development and refinement of our technology, ensuring that we deliver practical and sustainable solutions. The real reward lies in the tangible impact of our work — reducing deforestation, managing urban waste effectively, and contributing to a circular economy. It’s this mission-driven approach that keeps our team grounded and motivated.
Beyond paper, do you see other uses for leaf-based materials in the future — maybe packaging or even textiles?
Our USP (Unique Selling Proposition) is “Stylish recyclable packaging materials, produced from locally sourced green waste, for local environmentally responsible businesses.” So it’s not only about paper itself, more about packaging. One day it may be even textiles, yes, it’s possible.
Last one: if you could send one message to the traditional paper industry, what would it be?
The way it was before — won’t work anymore. Let’s unite efforts to reshape the paper industry.
If you’re curious to learn more about this startup, you can meet the founders live at the Greentech Festival in Berlin from May 20–22, 2025! We sincerely thank the founders for this inspiring interview.
Foto/Quelle: Releaf Paper